CNC Turning Parts Factories: Driving Precision in Metal Fabrication
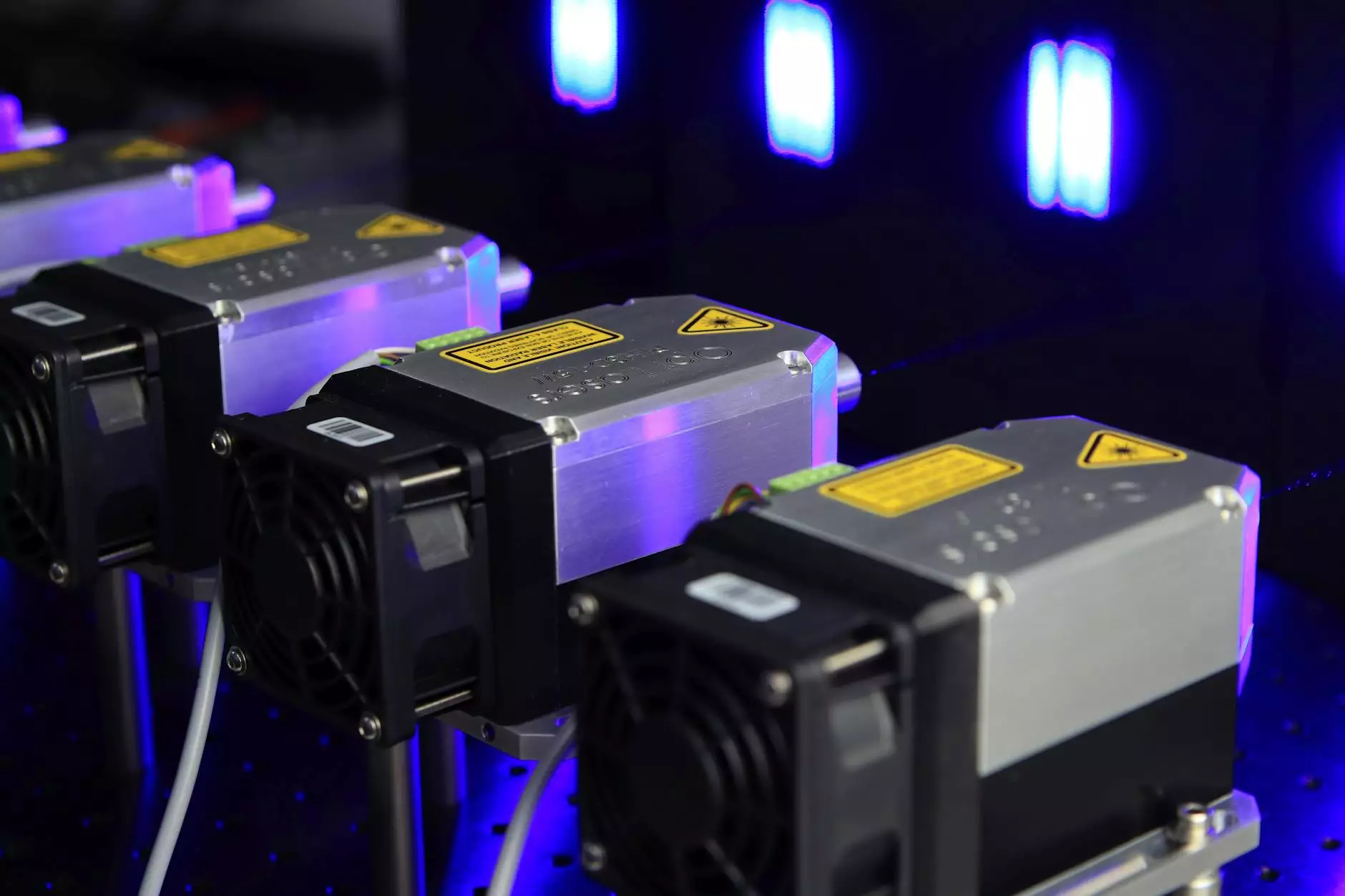
In the manufacturing sector, the significance of cnc turning parts factories cannot be overstated. These facilities play a crucial role in the production of complex components that are essential across various industries, including automotive, aerospace, and electronics. By utilizing advanced technologies and intricate processes, CNC turning parts factories ensure that components meet the highest standards of precision and quality. This article delves deep into the workings of CNC turning, the advantages it brings to businesses, and the future trends in this ever-evolving industry.
Understanding CNC Turning Technology
CNC, or Computer Numerical Control, refers to the automation of machine tools through the use of computer programs. The turning process involves rotating a workpiece against a cutting tool to produce cylindrical parts. This method is favored for its accuracy and efficiency, making it a cornerstone of modern metal fabrication. Here are the primary elements involved in CNC turning:
- Computer Programming: Operators input design specifications into a computer which controls the machine's operations.
- Workpiece Setup: The materials to be machined are securely attached to the spindle to ensure stability during the turning process.
- Machining Operations: The cutting tool, designed for specific geometries, removes material from the rotating workpiece according to predetermined paths.
Key Benefits of CNC Turning Parts Factories
CNC turning parts factories offer numerous advantages that make them an attractive option for manufacturers globally. Here are some of the most compelling benefits:
1. Enhanced Precision and Consistency
CNC machines provide a level of precision that is difficult to achieve with manual machining. Every component produced is identical, meaning that businesses can maintain strict quality control. This is essential in industries where even the smallest deviation can lead to significant problems.
2. Increased Efficiency and Productivity
With CNC technology, factories can operate continuously, with minimal downtime associated with setup time. This leads to faster turnaround times and the ability to handle larger production runs, meeting customer demands more effectively.
3. Flexibility in Production
CNC turning allows for quick adjustments in production processes. If a design needs to be altered, the change can be made in the program without needing significant retooling, thus adapting quickly to market changes or customer requirements.
4. Cost-Effectiveness
Although the initial investment in CNC technology can be high, the long-term savings are considerable. The decreased labor costs, reduced waste, and enhanced efficiency translate to lower overall production costs for businesses.
Applications of CNC Turning in Various Industries
The versatility of CNC turning makes it applicable in numerous sectors. Some notable applications include:
- Automotive Industry: Manufacturing precision components such as engine parts, gears, and bushings.
- Aerospace Industry: Producing lightweight and durable components critical for aircraft and spacecraft.
- Medical Devices: Crafting custom parts for equipment like implants and surgical instruments.
- Electronics: Creating enclosures and connectors for devices.
The Future of CNC Turning Parts Factories
As technology evolves, so does the landscape of CNC turning parts factories. Several trends are set to shape the future of this industry:
1. Integration of AI and Machine Learning
The incorporation of artificial intelligence and machine learning will enable factories to optimize their manufacturing processes. Predictive maintenance, quality assurance, and operational analytics will profoundly enhance productivity and reduce machine downtime.
2. Increased Automation through Robotics
Robotic arms are increasingly being integrated into CNC turning factories to automate repetitive tasks. This not only further increases productivity but also diminishes the risk of human error, leading to higher quality components.
3. Sustainable Manufacturing Practices
As environmental concerns rise, CNC turning factories will focus on sustainable practices. This includes reducing waste through optimized machining and selecting eco-friendly materials that minimize the ecological footprint of manufacturing processes.
Choosing the Right CNC Turning Parts Factory
When selecting a CNC turning parts factory, several factors should be considered:
- Technical Capabilities: Ensure the factory has the necessary machinery and technology to meet your specific requirements.
- Quality Assurance Processes: Look for factories that have robust QA processes in place to ensure the components you receive meet the required standards.
- Experience and Reputation: Research the factory's history and reputation in the industry. Customer reviews and case studies can provide insights into their reliability.
- Customer Support: A responsive and helpful customer service team can facilitate smooth communication and handle issues if they arise during the manufacturing process.
Conclusion: The Integral Role of CNC Turning Parts Factories in Modern Manufacturing
In conclusion, cnc turning parts factories are invaluable to the landscape of modern manufacturing. Their ability to produce high-precision, consistent, and cost-effective components has made them essential players across numerous industries. As advancements in technology continue, these factories are poised to enhance their contribution further, driving innovation and excellence in production. For businesses seeking quality metal fabrication services, embracing CNC turning is a powerful step towards achieving operational success.
For more information and insights, visit Deep Mould.